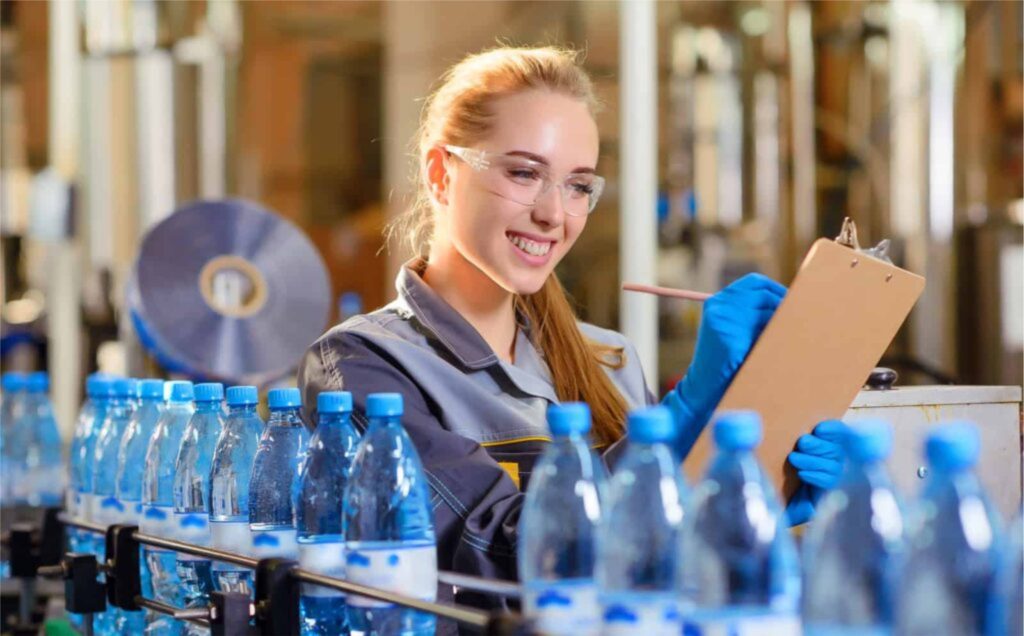
Predictive maintenance plays a pivotal role in preventing breakdowns in various industries, including the food sector. This proactive approach to maintenance leverages advanced technologies and data analysis to predict potential equipment failures before they occur.
In the context of the food industry, where hygiene and safety are paramount, the role of predictive maintenance is particularly crucial. This section explores the significance of predictive maintenance in preventing breakdowns and its specific applications in the food equipment domain.
1. Early Detection of Equipment Anomalies:
- Predictive maintenance utilizes sensors and monitoring devices to collect real-time data from food equipment.
- By continuously analyzing this data, deviations from normal operating conditions can be detected early on.
- Early detection allows for timely intervention and correction of issues before they escalate into major breakdowns.
2. Reducing Unplanned Downtime:
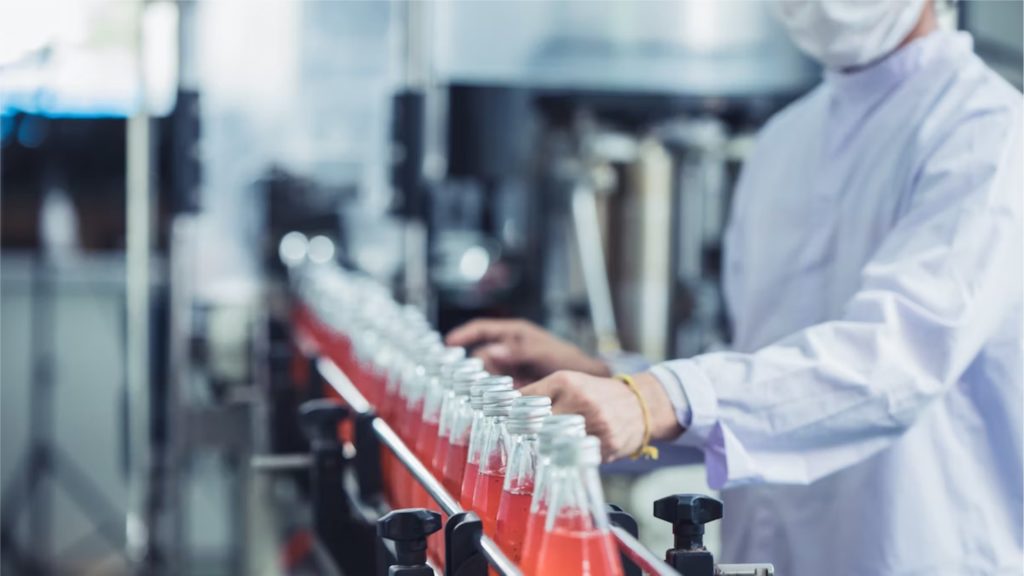
- Unplanned downtime can be costly and disruptive in the food industry.
- Predictive maintenance minimizes unexpected breakdowns by identifying potential issues in advance.
- This proactive approach enables scheduled maintenance during planned downtime, reducing the impact on production schedules.
3. Optimizing Maintenance Resources:
- Predictive maintenance helps optimize the allocation of maintenance resources.
- Instead of adhering to rigid time-based maintenance schedules, resources are deployed based on the actual condition of the equipment.
- This targeted approach ensures that maintenance efforts are focused on equipment that truly needs attention, maximizing efficiency and reducing unnecessary costs.
4. Preventing Contamination Risks:
- In the food industry, maintaining a hygienic environment is critical to preventing contamination.
- Predictive maintenance reduces the likelihood of unexpected breakdowns that could lead to contamination risks.
- Ensuring the reliability of equipment involved in food processing, storage, and transportation is essential for upholding hygiene standards.
5. Extending Equipment Lifespan:
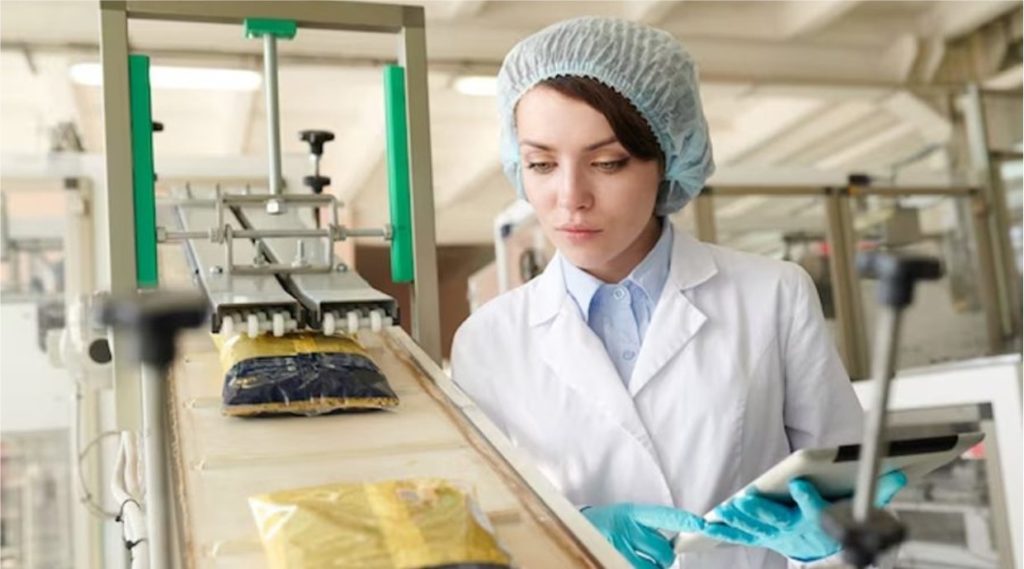
- Identifying and addressing issues before they escalate helps extend the lifespan of food equipment.
- Continuous monitoring and analysis of equipment performance allow for timely replacements or repairs of components nearing the end of their operational life.
- This proactive approach contributes to long-term cost savings by minimizing the need for premature equipment replacements.
6. Enhancing Safety Compliance:
- Adhering to safety regulations is a fundamental aspect of the food industry.
- Predictive maintenance assists in meeting safety compliance requirements by ensuring that equipment is consistently in optimal condition.
- Regular monitoring and documentation of maintenance activities contribute to a comprehensive safety management system.
7. Integration with Internet of Things (IoT) Technologies:
- Predictive maintenance often integrates with IoT technologies, allowing for real-time connectivity and data sharing.
- IoT-enabled sensors and devices provide a wealth of data, enhancing the accuracy of predictive analytics.
- This connectivity facilitates remote monitoring and immediate response to emerging issues.
In conclusion, predictive maintenance is a proactive strategy that significantly contributes to preventing breakdowns in the food industry. By harnessing the power of data analytics and technology, businesses can enhance operational efficiency, reduce downtime, ensure compliance with hygiene standards, and ultimately provide a safer and more reliable food processing environment.